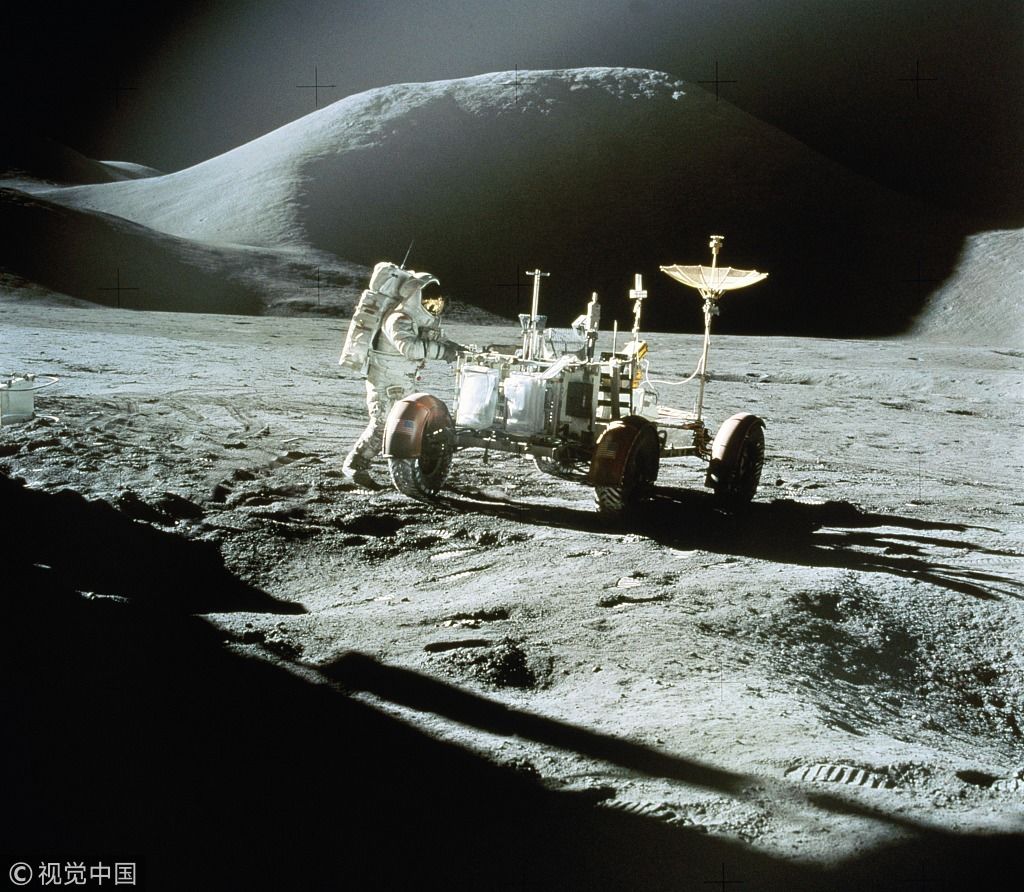
造车的确是一个比互联网产品难很多个数量级的工作,仅仅是打造「电池组」的复杂程度也许就能突破你的想象。
1971 年 7 月 30 日 22 时 16 分,「阿波罗」15 号飞船的登月舱在月球着陆。
这是人类的第四次成功登月,但与之前不同的是和两位宇航员一起登陆的,还有一辆精致的电动汽车——月球漫游者(Lunar Roving Vehicle),航天员大卫·斯科特和吉姆·欧文驾驶月球漫游者这辆四轮电动车完成了人类首次月球行驶。
这辆车的空载重量为 210kg,月球表面的重力约为地球的六分之一,所以它在月球上仅重 35kg。动力系统由 4 个车轮上的直流电机提供,电池是两块 36 伏的氧化银电池,续航里程约为 92km,帮助他们在月球上的哈德利月溪附近进行远距离的科考活动。
宇航员返回地球时「月球漫游者」被留在了月球上,成为了月球上为数不多的几个交通工具之一,直到今天。
这辆月球车被载入了史册,同样,打造这辆「未来交通工具」的通用汽车与波音公司也获得了更多的灵感。之后通用汽车发开了使用铅酸电池的概念车 Electrovette,1990 年又发布了 Impact 电动概念车。
直到 1996 年,通用汽车向市场推出了量产电动车 EV1。
可惜的是,这在当时并没有能够成为主流,但这让通用汽车对电动汽车有了更深入的了解。20 年后,时机成熟,2016 年,通用汽车推出了雪佛兰 Bolt 纯电动车,售价低于 4 万美元、续航超过 200 英里也让它成为了市面上主流的纯电动汽车之一,与火爆的 Tesla Model 3 抗衡。
在电池选择,研发方向上,通用雪佛兰 Bolt 和 Tesla 显然有着非常不同的路径,为此我们探访了通用汽车的电气化实验室,了解了更多关于电动汽车「电池组」的秘密。
电池的「抉择」
锂离子电池其实是一个技术相当成熟、应用极其普遍的产品,市场上有很多车用锂离子电池供应商。简而言之,在市场上很容易买到。
那么,为什么不采用市面上的成熟技术,为何还要坚持自主设计?自主设计的优势有什么?
- 量体裁衣:不同车型对于电池的具体需求是有所不同的。混合动力车型需要超高倍率性能的电池设计,纯电动车型更多需要考虑高能量密度的电池,而插电式车型更多需要倍率和能量的平衡。为每一种型号的车型提供最合适的电池,最好的办法是量体裁衣,而不是简单的从电池厂购买。有针对性地和供应商一起开发相应的电池体系,确保电池能满足成本、安全性和使用寿命的目标。
- 安全:电池研发的关键,是在安全性和电池性能之间达到平衡,其中,安全性更是重中之重。
- 掌握全局: 此外,只有亲身参与,才可以掌握整个电池生产环节中的细节,掌握更多数据,确立更为精确的数学模型,并不断在迭代中寻求优化提升的机会。
那么,接下来电池如何自主设计?
首先,是材料的选择。
三元材料的类型多样,如 111,532,622 等,可以根据不同车型要求选用对应的三元材料。比如纯电动车型电池选用高能量密度的三元材料,以使得在同等重量和体积下,可以储存更多的电量。通用汽车目前普遍采用的是三元材料的锂离子电池。
其次是,电芯封装的形式,也就是电池最后的呈现形态,也是电池设计中需要特别注意的。
通常情况下,电芯的封装形式有以下几种,圆铝壳、方形硬壳和软包。通用汽车除了采用硬壳封装之外,也会采用软包设计这一封装形式。软包电池使用铝塑膜通过焊接封装,轻便的铝塑膜,加上叠片工艺制作的电芯可以获得较高的电芯能量密度,软包的封装可以使得电芯和散热片完美贴合。
此外,正负电极极片的设计也需要根据不同车型来制作。包括电极的组成比例、厚度、压实密度、孔隙率以及正负极容量比例也至关重要。
通用汽车目前采用的电池极片设计是和供应商一起设计,开发验证完成的,以确保最优。
最后,特别值得提出的,是通用汽车特有的叠片式电池模块设计。
每个电池模块,由电芯、换热片、隔热片等组成。这样的设计,使得电池模块的热管理效率得到大大的提高。同时,电池单元与电池单元之间不会直接接触,这样即便某些电池单元间歇性地出现过冷或者过热的情况,也不会将温度传到给其它电池单元。相比其他的换热方案,这样的设计能更充分、更均匀对电池进行冷却或加热,始终处于最佳的温度区间。
设计完成后,最后需要电池验证。
难以想象的是,通用汽车每一款电池在投放市场之前,都会在电池供应商和通用汽车自己电池实验室里,经历 3-5 年的电芯验证测试。这么长的测试周期甚至比一些企业车型换代的时间都要长,在「新造车时代」更是很难想象。
仅仅在电池的验证环节上就花费 3 到 5 年的时间,就真的落后市场了?
其他很多车企不同,通用汽车并不是从外界购买电池,而是自主研发和电池供应商研发相结合,以确保这个「前瞻技术」在经历长时间的验证后仍然在竞争中保持领先。同时,也会不停地对现有技术进行升级和优化,缩短电池整体研发上所用的时间。
在这之后,完整的电池包和以及使用该电池包的车型还会继续在内部进行完整的工况测试。
电池「班主任」——BMS 电池管理系统
让这些电池高效协同地工作,是另一个需要解决的问题。
电动汽车的电池组系统往往是由成百甚至上千节电池组成的,例如雪佛兰 Bolt 就拥有 288 节电池。
而电池组系统符合「木桶效应」,也就是说系统的性能是由最差的那节电芯所决定的。因此只有准确监测到每一节电池、精确评估到每一节电池、并且高效的管理到每一节电池,确保所有电池保持一致的良好状态,才能够实现系统的高性能、长寿命、和安全的运行。
好的管理需要基于对真实信息的掌握,所以说灵敏的感知能力是电池管理系统实现最优控制的基础。
电池管理系统会监测到系统内每一节电池的电压,仅仅 1mv 的微小变化也能够被识别。同时,系统内每个区域都设置了温度传感器,使电池系统内热场分布情况能被充分感知。充放电过程中电池输入输出的电流都将实时被记录,电池管理系统还会监测电池的绝缘特性,确保电池高压与车身的充分隔离。
与此同时电池管理系统还会对这些「监测功能」再实时进行诊断和校验,一旦发现了故障,将会启动冗余方案。
接下来,电池管理系统就可以根据感知到的信息对系统状态进行深层次的评估。
- 荷电状态(State of Charge)评估,简单来讲就是电池剩余可用的电量。
和使用手机都有类似的经验,电动汽车的电池管理系统若不能精确计算出剩余电量,后果可不单单是打不了电话、刷不了朋友圈这么简单了。相比手机而言,电动汽车电池管理系统对电量的估算更为复杂,需要充分考虑温度因素、电池老化因素、电池一致性因素等条件才能更准确的获得真实的可用电量。
模型不仅能够评估当前剩余的电量,还可以准确计算电池当前功率边界(State of Power),也就是分析出当前电池可输出的最大功率,和电池可接收的最大功率。也就是告知车辆、充电设备电池此时此刻最大的能力。确保高性能的同时也兼顾了寿命。
- 健康状态(State of Health),也就是电池的寿命状态。为电池维护和替换提供有效的依据。
- 故障状态(State of Fault),电池管理系统会根据故障的严重性分级提醒用户,并分析出最优处理策略。
状态评估完成后,我们就需要真正的「管理」了。
因为电池有「木桶效应」,所以说保持电池的一致性至关重要。
电池的一致性可以认为是由两方面因素决定的,一方面,是「先天的」一致性,也就是在电池在生产制造过程中,通过先进的制造技术和工艺水平来保障电池的一致性。另一方面是「后天」的一致性,也就是通过电池管理系统,来继续维护这种一致性。所以电池管理系统强大的控制能力主要体现在维护电池一致性的能力。
首先电池管理系统需要维护所有电池荷电状态的一致性,也就是所有电池始终保持相同的荷电状态。电池管理系统要使最高荷电态的电池充电电流小于其他电池,最终使得所有电池在同一时刻充满。除此之外保证电池温度的一致性也是至关重要的。
对一辆电动汽车来说,仅仅是「电池组」的研发,就涉及到如此多的细节和要素,如果像通用这样仅仅是电芯就要经历 3-5 年的验证测试,对于这一辆车来说是怎样庞大的是一个时间管理系统,再涉及供应链和巨大的资金投入,甚至是未来的「智能」的加入,造车的确是一个比互联网产品难很多个数量级的工作。
本文感谢通用工程师孔德文(负责锂离子电池研发)、叶磊(负责动力总成技术研究)。
(图片来源于现场拍摄、通用官网)(编辑:早优夫斯基)